
Blog
Expert Advice
6 min read
8 Nov 2021
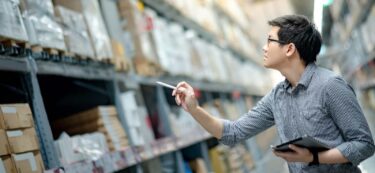
Blog
Expert Advice
6 min read
8 Nov 2021
For manufacturers and retailers alike, inventory management and replenishment are at the heart of operations. Products cannot be produced if the materials aren’t on-hand, and they can’t be sold if they’re not in stock. In other words, inventory health is a part of business that simply cannot be ignored.
Inventory replenishment, also known as stock replenishment, is the process of inventory moving from a supplier or reserve storage facility into a businesses’ primary storage facility for use or sale. The concept applies to the two main types of inventory – components or materials that are used in manufacturing and final products that are sold by retailers. In essence, inventory replenishment is the practice of making sure that the right quantity of items is available at the right time to allow for business as usual to continue.
There are a range of inventory replenishment strategies and models that revolve around different methods of reordering and receiving inventory, with each having unique pros and cons. Here’s everything you need to know about each, so you can make an informed choice between them.
First off, you need to understand what the common challenges in inventory management are. These are the problems that necessitate adopting a firm strategy on replenishment, and usually directly concern the bottom line:
Overcoming these challenges, usually achieved through the adoption of a more refined inventory strategy, can open you up to the many benefits of inventory management, including a decrease in operational friction, increase in profitability, and maximization of customer satisfaction.
So, what methods of inventory replenishment are there? Essentially, the choice can be boiled down to four main options, each of which has a range of possible variations. They are:
Periodic inventory replenishment is the practice of only checking whether inventory needs to be replenished at certain time intervals. For example, you might have a vague understanding that your inventory lasts for around three months before it begins to run dry, in which case, under a periodic ordering strategy, you would check inventory levels every three months. Upon checking inventory levels, you will either reorder to replenish stock levels or find that your stock levels are sufficient, in which case you wait until the next interval has elapsed before checking again.
Reorder point replenishment is based on stock levels themselves as the signal for replenishment, rather than time. It involves selecting a specific stock level that indicates it’s time to reorder new inventory. For example, if you typically have 1000 units of product in stock, you might set your reorder point to trigger when stock levels diminish to 200 units. You would then reorder 800 units, taking you back to optimal inventory health. It’s worth noting that a reorder point strategy requires robust real-time inventory tracking to work.
Also known as lean time replenishment, the top-off inventory replenishment strategy involves a much more fluid and opportunistic approach. It involves restocking inventory levels at opportune times when demand slows down, bringing inventory forward into primary storage to ‘top-off’ the primary inventory levels. It’s typically used in high-velocity sectors where it’s critically important to have healthy inventory levels when demand spikes, minimizing the chance of stock levels being low at the wrong time.
Demand-based replenishment is the final approach, involving a strategy that signals the need for inventory replenishment based on forecasted demand. Restocking under this approach will typically mean that the amount of stock ordered is just enough to meet demand expectations, necessitating a healthy level of safety stock to ensure orders don’t go unfulfilled if the demand forecasts are inaccurate. However, demand replenishment works best when you know your demand forecasting process is at least mostly accurate, as it can otherwise lead to issues with under or over-stocking.
The four main inventory replenishment strategies offer a diverse range of ways to manage stock levels that can be chosen depending on the unique needs of your business and your typical operational patterns. However, they’re not the only elements of an effective approach to inventory replenishment – there are other ways to optimize the process to minimize the risks posed by the inventory management challenges listed above. They include:
Not all types of inventory will have the same importance or impact on business, so it stands to reason that they might not all require the same replenishment strategy. That’s why, for businesses that have diverse types of stock on hand, splitting inventory into categories that determine the approach to replenishment can be a smart decision. For example, if you’re a retailer who sells both low and high-value products, you might find that splitting your approach to stock replenishment in two is best. This might take the form of low-value products being replenished using the top-off strategy, while high-value products are replenished through a reorder point approach.
Demand forecasting is the best tool you have in your arsenal to inform your inventory replenishment strategy. Theoretically, if your demand forecasting was 100% accurate, you would be able to order exactly the right amount of inventory at exactly the right time. That’s next to impossible, but it implies that the more accurate your demand forecasting, the more efficient your replenishment strategy can be. It makes sense, then, to aim to optimize your demand forecasting capabilities as much as possible, since the positive effects it can have on inventory replenishment are potentially highly lucrative.
One of the main challenges in effective inventory management is dealing with the uncertainty that comes as part and parcel of relying on suppliers. Long lead times and unfulfilled orders can both significantly affect your profitability if they disrupt your ability to meet demand, so it’s well worth putting a lot of care and attention into the process of selecting and reviewing your suppliers. And remember that even the most reliable suppliers will sometimes fall short of your expectations, so having a backup plan is never redundant.
Finally, making use of a sophisticated inventory management solution can help to bring order and efficiency to your approach to inventory replenishment, and the inventory management process as a whole. Features like real-time inventory tracking, access to safety stock supplies, and reduction of long lead times can all refine your ability to maintain optimal levels of inventory while also making best use of your working capital.
Industry
Inventory management is an essential process for almost every type of business. Inventory is often the largest current asset and…
Industry
As demand for the movement of goods across the globe and rapid delivery expectations become the norm, businesses seek ways…
Expert Advice
Inventory management plays a crucial role in the success or failure of any business, and the consequences of ineffective inventory…