What is inventory cycle time?
Inventory cycle time is the amount of time it takes to produce and deliver an order from a customer, usually measured in days. It essentially measures the speed at which a company can complete the manufacturing or assembly process from start to end, turning raw materials or components into a sellable product.
However, in practice, inventory cycle time means different things to different businesses. For a manufacturer, for example, cycle time measures the pace of production of products from raw materials. For retailers or distributors, though, inventory cycle time is more likely to be a measurement of how quickly inventory is sold (or turned over) after being received from a supplier.
Understanding how to measure inventory cycle time in your own business is important for a number of reasons. Most important among them is that the speed of order turnover and delivery – whether to a buyer within the supply chain or a customer at the end of the chain – is critical to customer satisfaction. And optimizing inventory cycle time can bring about efficiencies elsewhere, too, including by reducing the cost of inventory carrying cost – a critical element of any strong inventory management strategy.
How to measure inventory cycle time
The method used to measure inventory cycle time is simple, but it varies slightly depending on if you sell products within the supply chain or to final retail customers.
For manufacturers, inventory cycle time is also sometimes known as order cycle time. Typically, it’s represented as the average time between any two orders shipped, and the order cycle time entails several composite parts. It can generally be split into the ordering phase, production phase, and delivery phase. The amount of time it takes from starting the ordering phase (ie. placing the order for raw materials or components) to ending the delivery phase (ie. successful receipt of the products by the buyer) is the inventory cycle time.
As an example, if a manufacturer has an ordering phase that takes 10 days, a 15 day production phase, and a delivery phase of 5 days, their total inventory cycle time is 30 days.
For retailers, the inventory cycle time measurement is a little different. To start with, there is no production phase, as appears in the manufacturer’s inventory cycle. Instead, cycle time can be measured as the time between receiving products from a supplier to those products being sold, or turned over. It can be calculated either for each individual product sold, or for a batch of products as a whole.
For example, a retailer that receives an order of 100 products can measure inventory cycle time of one of those products (the time between the date of the product being received and the date it gets sold) or the inventory cycle time of the entire order (the time between the date of the products being received and the date the final product from the order is sold).
Takt time as an alternative
Inventory cycle time is a retrospective measurement, in that it can only be calculated after the inventory has already completed the cycle. That means it’s not very useful as a KPI when viewed in isolation as it lacks critical consideration of how the cycle time matches up to customer demand. Therefore, when trying to make improvements to inventory cycle time, it’s useful to also consider a metric called takt time.
Takt time adds customer demand into the equation and can essentially be used to set production targets. It is a formula that calculates the required rate of production (or inventory cycle time) to effectively meet customer demand. You can calculate it with the simple formula below:
Takt time = Total available production time / Average customer demand
For example, if a business has 100 hours a week to spend on production and receives an average of 50 orders per week from customers, their takt time would be 2 hours. This means that they need to produce one unit an hour, on average, over the course of the week in order to meet demand.
This figure can be compared to current inventory cycle time, with the difference between the two representing either overproduction (products being made at a faster rate than they’re ordered), or underproduction (orders being placed at a faster rate than production can keep up with). The insights gained from comparing these two metrics can help you to set targets – giving you a clear indication of just how much inventory cycle time has to improve in order to properly meet demand, for instance.
Optimizing inventory cycle time
Modern commerce is increasingly defined by speed – with the tone set by retail giants like Amazon who boast lightning fast delivery times. Keeping your customers waiting is now less viable than ever, and fulfilment times that lag behind the competition can seriously inhibit any commercial edge you have.
On the other hand, though, this change in consumer expectation also means that, if you can speed up your production time and offer quick turnarounds to customers, you’re able to punch above your weight and take on even the biggest competitors in the market. This is why taking inventory cycle time optimization seriously is so important.
And there are a broad range of potential optimizations that can be made to the processes that contribute towards inventory cycle time, including:
- Utilizing inventory management software – Digital inventory management solutions can help you to reduce inventory cycle time in many ways. Arguably the most important, though, is its ability to massively increase the visibility you have over inventory at all stages of the inventory cycle process. This improved visibility can enable you to identify inefficiencies in the inventory cycle and work towards resolving them, resulting in a decreased total inventory cycle time.
- Building strong supplier relationships – Suppliers can contribute significantly towards inventory cycle time, with their own processes in turn affecting yours by limiting the speed with which you can restock or move on with production. Prioritising building strong relationships with suppliers, usually made easier with supplier management software, can ensure that you are getting their best performance and maximizing the longevity of the relationship.
- Optimizing production – Finally, and most obviously, making improvements to the actual production process that typically takes up the majority of the inventory cycle process can see cycle time reductions. Techniques to achieve this range from implementing automation on the production line to reviewing management styles. The goal is to cut down on any inefficiencies in the production process, ensuring each product gets produced as quickly as possible.
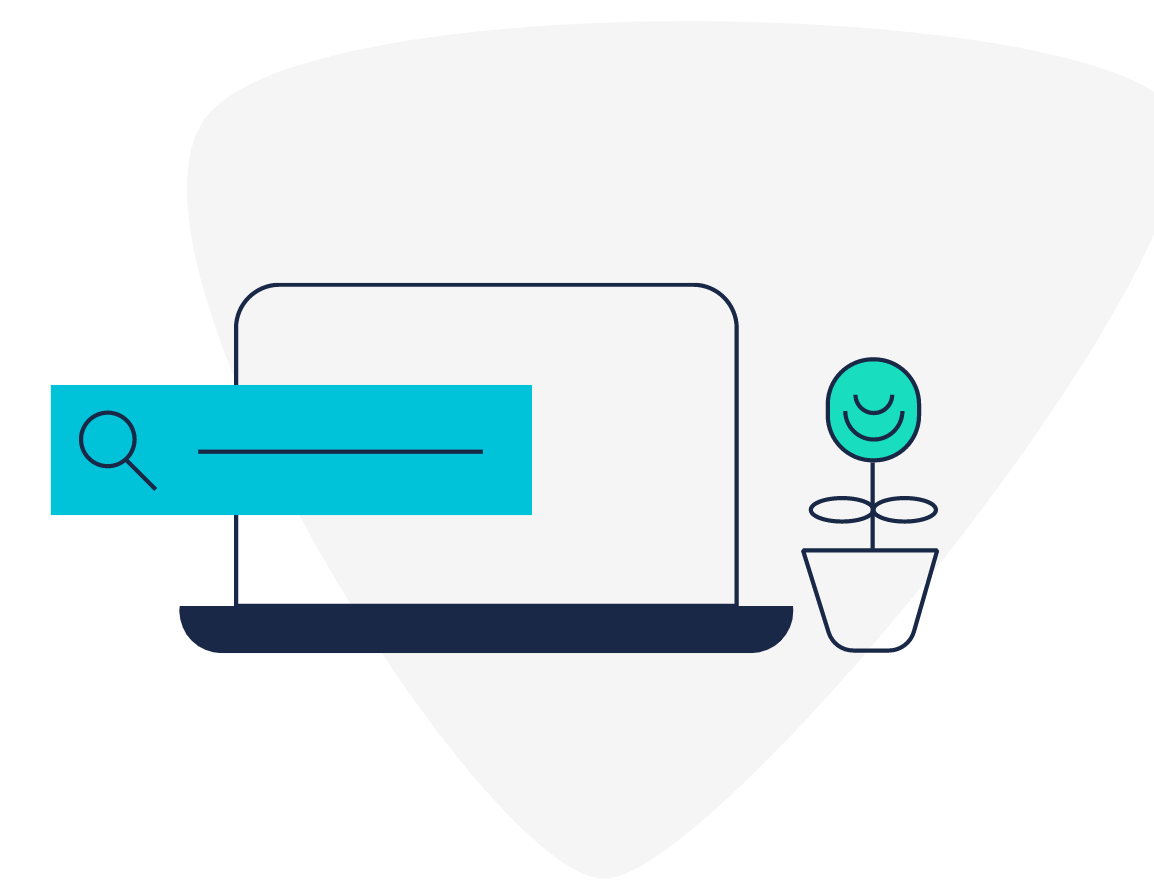