What is a lean supply chain?
A lean supply chain is an approach to supply chain management that aims to minimize waste and maximize value creation throughout the entire supply chain process. The core aims of a lean supply chain are to streamline operations, reduce costs, improve quality, and, ultimately, enhance customer satisfaction.
In today’s competitive and dynamic business landscape, companies are constantly seeking ways to optimize their operations and gain a competitive edge. Adopting some or all of the principles behind lean supply chain management is one way of doing that. A lean supply chain is, in essence, a supply chain that’s operating at maximum efficiency.
It’s often characterized by qualities like a small but effective supplier base, low stock levels held in warehousing, and stringent quality control processes. These efficiency-focused approaches to regular supply chain activities help businesses to increase the value that their supply chain delivers, helping them to boost overall operational efficiency.
Lean vs agile supply chains
Lean supply chains can be seen as one end of the spectrum of supply chain strategies with agile supply chains at the other. Whereas lean supply chains prioritize efficiency over other factors, agile supply chains are primarily concerned with resilience and responsiveness.
The agile methodology prioritizes flexibility and adaptability to changing market factors, both within the supply chain and external to it. This is done to reduce the supply chain’s vulnerability to supply chain risks, which can, in turn, cause disruptions that affect profitability. However, this resilience comes as a trade-off; an agile supply chain will inherently be less efficient because it is geared to be more resilient.
Agile supply chain management often involves making heavy use of techniques like inventive, flexible inventory management solutions, demand forecasting, and intentional redundancy in the supplier base.
The principles of lean supply chain management
Waste reduction
In the context of a lean supply chain, waste refers to any activity that doesn’t add value to the end product or service. Lean thinking considers ways to reduce waste throughout the supply chain, including overproduction, waiting, transportation, unnecessary inventory, and defects.
By systematically identifying and eliminating these sources of waste through lean supply chain management, the supply chain becomes more efficient and responsive. This can result in faster inventory cycle times and reduced costs.
Continuous improvement
Lean supply chains are often built on the principle of continuous improvement. This approach encourages organizations to engage all employees in identifying problems, suggesting solutions, and implementing improvements.
Through ongoing iterations and small incremental changes, businesses can achieve higher levels of efficiency and quality throughout their supply chain.
Reactive production
In contrast to traditional push-based production systems that produce goods based on forecasts, a truly lean supply chain operates on a pull-based model. This means that production is triggered by actual customer demand, minimizing the risk of overproduction and excess inventory.
Pull-based production ensures that resources are used efficiently, and customer needs are promptly met. It also reduces inventory carrying costs, which adds further value to the approach.
Benefits of a lean supply chain
Implementing lean principles in the approach to supply chain management can yield several significant benefits for businesses, including:
Cost reduction
A lean supply chain reduces costs associated with excess inventory, overproduction, transportation, and inefficient operations by eliminating waste and streamlining processes. These cost savings can enhance a business’s profitability and competitiveness in fierce markets.
Improved efficiency
Lean supply chain principles enable organizations to optimize operations, improve cycle times, and enhance resource utilization. This efficiency leads to increased productivity and encourages a culture of efficiency, which can mean goods pass through the supply chain faster.
Minimized waste
As a by-product of the focus on efficiency, lean supply chains are inherently less wasteful than agile ones. This reduces costs and can also be a factor in meeting ESG goals, an increasingly important consideration for modern businesses.
Enhanced quality
Lean methodologies place a strong emphasis on defect prevention and error-proofing. By continuously improving processes, reducing variability, and focusing on quality control, businesses can deliver higher-quality finished goods to their customers.
Increased customer satisfaction
A lean supply chain is customer-centric at its core. By eliminating waste and delivering products or services based on actual demand, businesses can meet customer expectations more effectively, leading to higher satisfaction and loyalty.
The downsides of lean supply chain management
However, not everything about the lean supply chain management approach is positive. The methodology can have the following downsides.
Risk of stock-outs
Businesses that use lean supply chains are more at risk of stock-outs than those that use agile supply chains. This is partly because they typically rely on fewer suppliers, meaning that problems with a supplier can cause serious issues with production schedules. However, it’s also a symptom of their avoidance of reserving safety (or buffer) stocks, which means that they can be caught unprepared for sudden surges in demand.
Vulnerability to external risks
External risks, such as natural disasters, pandemics, and wars, can also cause serious problems for businesses that use lean supply chains. Without redundancy in their supplier base, they rely on their suppliers’ continued operations to fulfill demand. If their suppliers suddenly encounter problems, it can ripple through the supply chain and result in halted production.
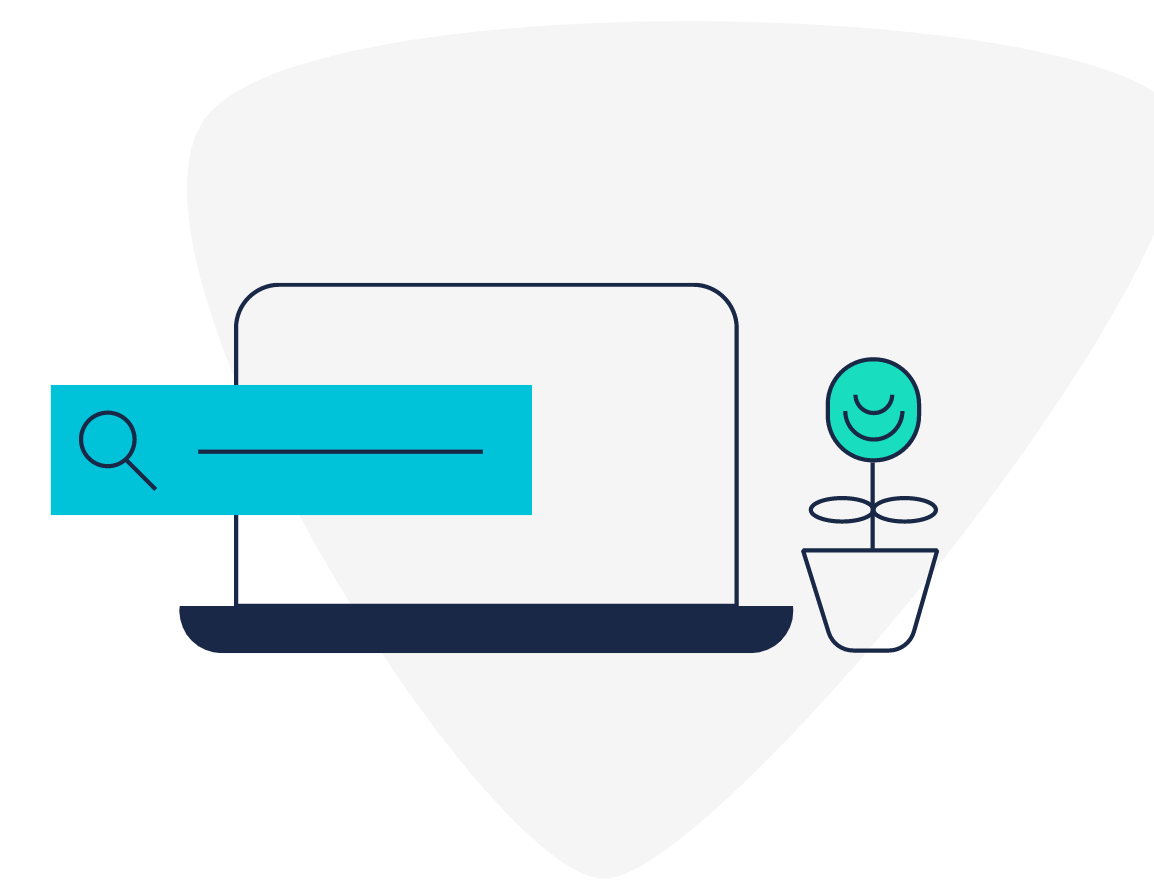