
Blog
Expert Advice
8 min read
2 Mar 2023
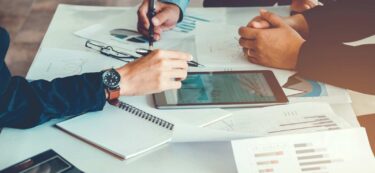
Blog
Expert Advice
8 min read
2 Mar 2023
Uncertain or challenging market conditions require more sophisticated approaches to how supply chains serve business needs. Here’s a guide to the principles of strategic supply chain management.
The tumultuousness of the modern macroeconomic and geopolitical environment exposes companies to various supply chain risks. Monetary inflation, rising commodity prices, economic turmoil, and fluctuations in demand all have the potential to put a strain on global supply chains.
Against these uncertain and unpredictable conditions, businesses have a greater incentive than ever to optimize their supply chains for resilience and stability. A stronger, more flexible supply chain can be a key component in helping a business achieve its aims, whether that’s growth, reliability, or any other business objective.
The first step in this optimization is acknowledging the importance of a more strategic approach to supply chain planning and management.
A supply chain strategy defines a business’s approach to managing the flow of goods and services throughout its supply chain. It covers the full range of supply chain processes, from procuring raw materials to delivering the finished products to customers.
Supply chain strategy differs from supply chain management in that it’s more concerned with the ‘why’ than the ‘how’. A strategic approach to supply chain operations seeks to align the supply chain components to meet specific, predetermined business goals. These might include improving efficiency, reducing net costs, or minimizing order fulfillment time. In other words, strategic supply chains aim to align with broader business strategies.
Strategic supply chains differ from non-strategic supply chains. The latter is not necessarily planned and managed to achieve a specific outcome. Instead, it is handled with a light touch, often optimized only to the point where it works on a fundamental basis.
The following hypothetical example should help you better understand the difference between a strategic and a non-strategic supply chain:
Having recently acquired two new companies – the Zenith Precision Machining Organization and the Nadir Tool & Die Company – the Stellar Corporation has reviewed the different strategies of both companies regarding their supply chains.
The contrast between these two extreme examples illustrates the differences between a carefully designed and planned supply chain strategy and a poorly planned and non-strategic one.
The implication of Zenith Precision Machining’s supply chain setup and approach to management implies a focus on resilience. They have a diverse supplier base of vendors who have been carefully chosen and are constantly assessed. They have a sophisticated inventory management process that helps them better monitor the supply chain’s risk.
Nadir Tool & Die, on the other hand, doesn’t appear at first glance to have a strategy. Their supply chain is organic and somewhat antiquated. It doesn’t serve any particular aim except to fuel manufacturing. The lack of strategy opens the company up to significant risk.
Rather than attempting to adopt a ‘one-size-fits-all’ model, companies seeking better outcomes from their supply chain activity need a supply chain strategy that considers the factors unique to that business, including what sector it exists in or what unique aims it’s interested in achieving.
This requires a certain level of bespoke tailoring. No supply chain model perfectly suits a specific company ‘off-the-rack’. Instead, companies adopt a ‘template’, the outline of a supply chain strategy, and tweak it to suit their objectives.
There are plenty of choices regarding supply chain models, but there are two main basic templates.
A lean supply chain strategy aims to turn raw materials into finished goods or services with minimal waste and loss. In other words, it pursues maximum efficiency. This can be achieved by streamlining processes, eliminating unnecessary expenditures, and minimizing inventory and holding costs. For companies with readily-available raw materials or components, who can switch suppliers easily, this can remain an attractive option – even in uncertain times.
A resilient supply chain is designed to survive in challenging conditions by adapting quickly to unanticipated events. It’s generally characterized by supplier redundancy and high levels of safety stock. Although this approach may lead to higher costs, it has clear benefits for companies, especially those vulnerable to supply chain disruption or whose components are particularly specialized. The more resilient the supply chain, the more the company is protected from major disruption.
A supply chain strategy affects how a business plans its supply chain and the approach taken to execute and manage that plan.
Planning is hugely important in pivoting towards a more strategic supply chain. The planning process involves the following steps:
The success of a strategic supply chain is also heavily influenced by how effectively it is deployed and managed. Businesses looking for better alignment between their supply chain activity and their specific business aims should ensure they’re doing the following:
A more strategic supply chain can deliver a number of benefits, which are compelling in all circumstances but particularly important when market conditions turn challenging. They include:
In order to work together and achieve the same goals, the internal teams of a business need a clear and consistent vision rather than vague objectives. With solid and well-defined supply chain strategies, businesses can ensure consistency across all departments and ensure their teams are working from the same playbook.
By considering its supply chain strategy more deeply, a company can ensure that its supply chain activities – which make up a large part of overall business operation – are working towards the business’s aims, helping it achieve greater financial stability and stronger growth, and increased profitability.
Finally, when formulating a supply chain strategy, the business must decide what the supply chain needs to deliver, how these objectives will be achieved, and how performance should be measured against the chosen criteria. The business can then review performance more easily and adjust its strategy to drive greater efficiency and resilience.
Industry
The sustainability of supply chains has become increasingly important to businesses in recent years, as consumers become more concerned with…
Expert Advice
Supply chain finance – also known as reverse factoring (and abbreviated as SCF) – is a way of offering your…
Expert Advice
Inventory management is a core procedure in most businesses’ daily operations, ensuring that goods and materials are where they ought…