
Blog
Expert Advice
8 min read
26 Jun 2023
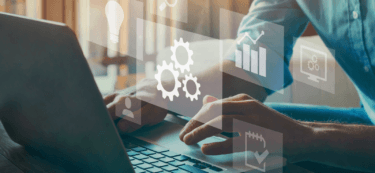
Blog
Expert Advice
8 min read
26 Jun 2023
An effective and efficient supply chain is vital to the success of any business. It contributes significantly to overall financial health, increases resilience against adverse conditions, and plays a vital role in ensuring products are delivered on time to customers.
By focusing on improving their supply chain processes, businesses can improve product quality, avoid inventory shortages or oversupply, increase customer satisfaction, protect against supply chain risks, and reduce costs.
A supply chain represents the flow of goods, materials, and services that underpin business operations, from sourcing raw materials to delivering finished goods. Each business has its own supply chain and is responsible for constructing and managing it to suit its unique objectives.
Involving suppliers, manufacturers, distributors, and customers, the supply chain process can be broken down into the following stages:
One of the most important steps in the supply chain process comes before it’s up and running. That step is planning and establishing a supply chain that is finely tuned to your specific business needs, the sector you operate in, and the market you serve.
During this step, you first need to decide on supply chain objectives and specify the metrics that will be used to monitor progress toward them. Then, move on to build your supply chain to suit those metrics. This includes supplier sourcing – the process of choosing suppliers to fulfil your need for goods and materials while also considering how well they serve your specific aims.
At this initial stage, you can also consider how to achieve visibility over inventory flowing through the supply chain, and determine how you’ll integrate other technological processes like cash flow and demand forecasting.
With the sourcing of suppliers complete and the foundation of your supply chain well established, the supply chain process proper begins with purchasing raw materials and components.
The purchasing process formalizes the way in which a company buys goods and services, meaning that spending can be carefully managed and tracked. By having guidelines in place for every part of their purchasing process, from negotiating contracts to approving purchase requests, companies can ensure that their purchasing practices match their business objectives while increasing efficiency and minimizing risk.
The manufacturing process involves taking purchased raw materials and components and developing them into finished products. Although some manufacturing processes can be straightforward, modern manufacturing may include several steps that require products to pass through different facilities at various stages of completion.
At this stage, the priority is to make sure that the materials or components supplied meet the required standards. Rigorous measurement of supplier performance, in terms of order fulfillment rates, price accuracy, and quality of goods, act as metrics to assess them against. It’s also increasingly common to track the flow of goods and materials throughout these steps, to facilitate inventory visibility.
When complete, the final products must then be stored, so they’re ready for distribution to customers. Different options are available for this, each with their own pros and cons. The balance to be struck is between the cost of holding inventory and the speed with which you can fulfil orders.
Using inventory management techniques to oversee both raw materials and finished products, you can take steps to optimize stock levels and improve how well your inventory warehousing and product delivery process serves your business objectives.
The distribution process involves the movement of finished products from storage to the end customer. Success here revolves around moving the right products, in the right quantity, on time, and to the correct location – all while managing costs.
Depending on your business goals and the market in which you operate, you can either deliver products directly to customers or distribute them indirectly through partners or third parties such as agents, wholesalers, or retailers.
Choices made at this stage of the supply chain process influence inventory cycle times and costs. Choosing the right distribution partners and tools can both drive efficiency and increase customer satisfaction levels.
Inevitably, there will be occasions when customers return products. When goods are returned, they need to be checked to see if they meet the criteria for returns and refunds. They are either repackaged for resale or disposed of, with the relevant data entered into an inventory system.
Refunds should be issued as quickly as possible, as customer relationships can be severely damaged if this process is mishandled. A smooth process, on the other hand, can strengthen customer relationships.
The supply chain process is a dynamic part of business operations, each stage of which can be optimized and refined to bring about efficiency. These are some of the most viable methods for improving the way your supply chain operates.
First and foremost, it’s essential that you adopt a supply chain model that fits both your unique objectives and the sector in which you operate.
The main dichotomy in supply chain models is between lean and resilient. Lean supply chains seek to eliminate unnecessary expenditure, turning raw materials into finished goods with minimal waste and loss. Resilient supply chains are designed to adapt quickly to unanticipated events by holding safety stock and having a degree of supplier redundancy built in. The former approach is geared to ‘just-in-time’ inventory practices, and the latter ‘just-in-case’.
The lean approach relies on all the supply chain steps functioning almost perfectly. Without safety stock, disruption from a single supplier could cause production to halt almost immediately. On the other hand, a resilient approach will come with greater storage costs and a greater risk of obsolescence while tying up more cash.
Efficient and effective supply chain management should include all the different supply chain steps, including sourcing and selecting suppliers, procurement, supplier management, inventory tracking, and the delivery of finished products or goods.
Supply chain management (SCM) software can help in the planning, execution, and tracking of operations, thereby streamlining the entire process. SCM software can coordinate and consolidate these various supply chain steps by addressing the discrete stages of supply chain management, such as sourcing and development, ordering, production, inventory, financial management, and distribution.
By enabling different departments to work together and make better-informed decisions, SCM software can also help businesses reduce costs, increase profitability, and maximize their working capital.
The different stages of the supply chain present various risks, which can arise due to internal and external factors.
Internal risks include poorly planned processes, inadequate forecasting capabilities, disruptions such as staff shortages and software issues, and a lack of contingency planning. External supply chain risks, meanwhile, can include problems with suppliers, shortages of raw materials, demand volatility, and environmental and political disruption.
By establishing a thorough risk assessment procedure and analyzing supply chain risks regularly, a business can identify potential problems before they arise. Companies will therefore be better placed to mitigate any operational challenges – from major supply chain breakdowns to minor disruptions.
Expert Advice
Use these 10 supply chain KPIs to measure your supply chain performance and find opportunities for optimization.
Expert Advice
Supply chain finance – also known as reverse factoring (and abbreviated as SCF) – is a way of offering your…
Industry
The sustainability of supply chains has become increasingly important to businesses in recent years, as consumers become more concerned with…