
Blog
Expert Advice
8 min read
15 Nov 2021
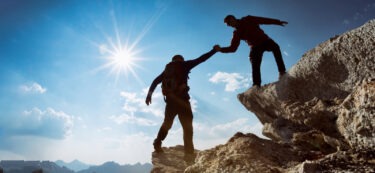
Blog
Expert Advice
8 min read
15 Nov 2021
Complex supply chains, by their nature, always involve an element of risk. A business that makes up a part of a supply chain will have to rely on other companies in order to operate. This inherently comes with potential dangers.
Given that global supply chains, and the complexity that comes along with them, are increasingly common, supply chain risks are more important to consider than ever before. They come in many forms, but the risks posed by suppliers themselves are some of the most critical. Failing to consider these supplier risks ahead of entering into an agreement with a new supplier, or neglecting to continually monitor their risk profile throughout your relationship, can lead to surprises that can significantly impact your supply chain’s health, and therefore your operations.
That means it’s hugely important to properly evaluate a supplier’s risk profile, continually make strides to manage supplier risks, and minimize the chance of a risk catching you unaware. Here’s a guide to understanding what risks suppliers can pose, and how you can mitigate them to strengthen your supply chain resilience.
Supplier risk refers to the possibility that a supplier (or vendor) may have a negative impact on the activity of a buying company. Supplier risk management has been a major issue for procurement departments for years as these risks can severely limit operations.
The failures of a supplier may lead, for example, to late delivery, disrupting the supply chain and affecting your company’s operations. Another risk may be that the quality of products supplied is worse than expected and so the buying business’s own products suffer in quality. A further risk may be that the supplier goes out of business, resulting in difficulty sourcing a particular component, perhaps due to it being particularly specialized.
Consequently, an organization may choose to contract multiple suppliers for the same component, or instead engage in more efficient risk management strategies.
There are many possible risks for any company, dependent on its activity, or the types of purchases it needs to make. Generally though, there are considered to be four main categories of supplier risk:
A key element of risk management is understanding, evaluating and then mitigating the correct risks. Classifying risks, then, is a key stage in this process and one common way of approaching this is to categorize known and unknown risks.
A known risk is as the name suggests – the organization is aware this risk exists. A known risk can be measured and quantified. An example would be the risk of a company losing some of its customers to its competitors. Virtually every business in the world is conscious of this risk and can reasonably quantify the likelihood of this happening, as well as the financial impact. A known risk can be investigated ahead of time and mostly avoided by choosing a different supplier.
An unknown risk tends to be more dangerous as they are unexpected and it is difficult to anticipate the damage they will cause. For instance: extreme weather conditions, a tornado or an earthquake. A pandemic is another example.
However, companies should not completely give up on these risks. Despite how difficult they can be to predict, it’s important to have a continuity plan in place to help manage these events when they do happen.
Supplier risk cannot, unfortunately, be entirely eliminated. That makes it all the more important that the necessary steps are taken to manage it. It is vital to do your due diligence, evaluating the risk of any key suppliers to determine whether they pose a threat to your operation, how easily they could be replaced if needed, and how much it could affect you if things go wrong.
Here is a step-by-step process for carrying out a supplier risk assessment:
The first step in evaluation is to identify what risk level is actually present. It can help to establish a framework that helps you do this – think about which risks are of concern to your business and which aren’t.
Also consider that the suppliers that are most critical to the operation of your business require the closest attention. It’s much more important to assess the risks posed by a major raw material supplier than for a tangential software provider, for instance.
This is crucial as the average business may have hundreds, if not thousands of suppliers. Conducting an assessment on every supplier and every risk may not necessarily be the best use of resources.
Once you’ve outlined what the potential risks and suppliers you need to assess are, you can move on to assessing them. One method of doing so is to assign a likelihood score to each risk for each supplier you’re assessing to get a complete picture of their total risk profile. This step can also involve assessing what the likely fallout of the risk occurring would be, and how you would manage it.
Risks don’t go away just because you’ve assessed them – even once you’ve decided to partner with a supplier, make sure to continue monitoring the risks you’ve already identified. Tracking their risk profile over time can help you to understand how they manage their own risks.
Unfortunately, risk management is not a static process. Known risks can change over time, while unknown risks can of course occur when you least expect them. Further, while evaluating a supplier’s risk profile is a crucial step, it is all for naught if there isn’t then action taken and policies implemented in order to manage that risk on an ongoing basis.
Analysis can only go so far. Outside of the quantitative risk assessment process outlined above, generally understanding your suppliers and building strong relationships with them can be a good way of preparing for unknown risks. Utilizing supplier relationship management solutions can help to meet this end.
Developing a culture of risk-awareness can ensure that unknown risks can be caught and countered more quickly. This spreads the burden of risk management amongst the people it concerns, and gives everyone a better opportunity to combat it.
Building anti-risk policies into your daily operation can prepare your company against unknown risks – this could include better internal training, proper access controls on sensitive software, and/or double-checking systems.
There is a growing threat of cyber threats and the correct digital training for all staff, as well as adoption of risk-averting software, and access controls can help avoid cyber risks, both internally and externally.
Expert Advice
Across the globe, there are four emerging VAT trends which suggest a need for adaptation.
Expert Advice
For manufacturers and retailers alike, inventory management and replenishment are at the heart of operations.
Expert Advice
The high stakes process navigated by the accounts payable department is deserving of effective management.