
Blog
Expert Advice
8 min read
6 Sep 2022
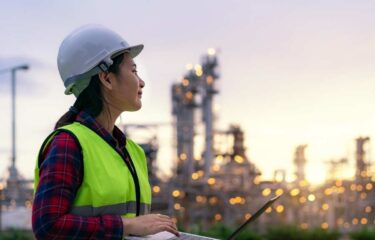
Blog
Expert Advice
8 min read
6 Sep 2022
For many companies, the production of finished goods from basic materials is key to operations. But those goods and materials, referred to collectively as inventory, can be difficult to manage efficiently – especially at scale.
Ineffective management of inventory can be extremely harmful to operational success. If a company finds itself with too little inventory, it may be unable to continue manufacturing or shipping products to match demand. Too much inventory and it will suffer from storage costs that are higher than necessary, reducing the amount able to be spent on fueling growth.
Getting this formula right – ensuring that inventory is always available when needed, but never a burden – is the central aim of inventory management. But, to complicate matters, there’s more than one inventory management strategy to choose from.
Inventory – generally consisting of finished goods, products still in the manufacturing process, and raw materials – needs to be managed appropriately for a company to fulfill orders on time, keep costs under control, and drive growth.
Inventory management is the process of doing just that. It’s a highly flexible operation that dictates how a company orders, stores, uses, and sells its goods and materials.
Making improvements in the way inventory is managed – in other words, having the right products and materials at the right time in the right place – can increase the resilience and efficiency of the supply chain, resulting in lower costs, optimized production, and faster sales.
More efficient inventory management can thereby accelerate the company’s growth, turning inventory into cash more quickly to increase working capital.
But there is a range of inventory management strategies and techniques that companies can make use of, and choosing the right one is a critical part of achieving success.
The goal of an inventory management strategy is to optimize the management of raw materials and finished products to meet the unique needs of the company. These needs may include ensuring that the company has enough product and materials to fulfill orders, fulfilling orders to a certain timeframe, or minimizing storage requirements.
With inventory management strategies, there is no ‘one size fits all’ approach. Different approaches are suited to different types of businesses, depending on their business model and their working capital goals.
Before moving on to look at specific inventory management techniques, it’s first important to understand the different ways of carrying out inventory counts, or measuring inventory. There are two main accounting methods to consider: periodic and perpetual:
There are various inventory management strategies, and each one operates differently and has diverse pros and cons. Common inventory management techniques include the following:
Economic order quantity (EOQ) is a metric that looks at all costs related to the purchase and delivery of goods and materials, including discounts and warehousing, while at the same time factoring in demand for the product.
One popular formula for calculating the economic order quantity is:
EOQ = √ [2 * Annual demand in units * Average order cost / Holding costs per unit per year]
Buying in bulk (also known as ‘just-in-case’ inventory purchasing) is where a business buys large quantities to supply a forecasted demand. This approach relies on the assumption that buying and receiving inventory in bulk is almost always cheaper.
The just-in-time (JIT) inventory system is an inventory management technique designed to minimize waste and increase efficiency by receiving goods only when production is scheduled to begin. For it to work, suppliers need to be extremely reliable, and production must be steady and problem free.
Safety stock is a method whereby companies deliberately order more inventory than they need. Some can then be set aside as safety stock in order to protect against future stock outages.
Safety stock comes at a cost. However, this can be mitigated with an inventory ownership service such as Taulia’s Inventory Management software solution, whereby Taulia can procure, own and hold safety stock near your destination.
ABC (also known as selective inventory control) categorizes inventory into different classes – typically A, B, and C – according to their importance. Different inventory management strategies are then adopted for each class.
Choosing the right inventory management approach means understanding how inventory impacts your business: Can you measure inventory constantly or just occasionally? Are product demand and purchasing costs stable or fluctuating? Are a few key products produced, or does your company produce thousands?
Both shortages and excesses of inventory can have serious consequences for a business. As such, improving inventory management can bring multiple benefits, from minimizing costs to guarding against fluctuations in supply and demand.
Choosing an effective inventory management system is one step that can help companies drive positive change. A system that tracks and manages inventory as it moves through the supply chain can help companies improve visibility over the movement of goods and materials, pinpoint inefficiencies, and ensure that the chosen inventory management approach aligns with the company’s cash flow needs.
Expert Advice
Inventory management is a core procedure in most businesses’ daily operations, ensuring that goods and materials are where they ought…
Industry
Inventory management is an essential process for almost every type of business. Inventory is often the largest current asset and…
Expert Advice
Inventory management plays a crucial role in the success or failure of any business, and the consequences of ineffective inventory…